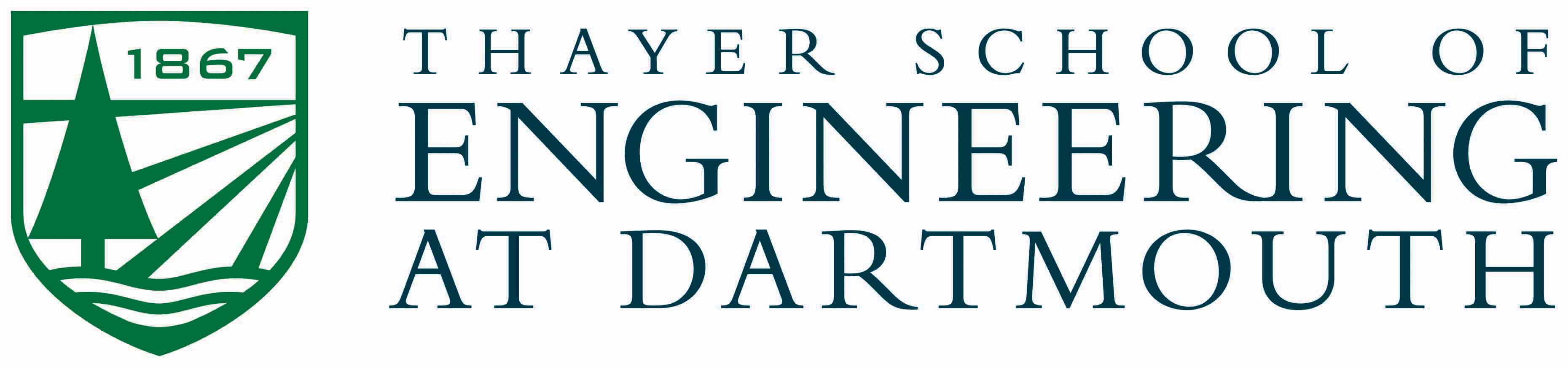
ENGS 89/90 Reports
Degree Program
B.E.
Year of Graduation
2019
Sponsor
Hypertherm
Project Advisor
Laura E. Ray
Document Type
Report
Publication Date
Winter 3-1-2019
Abstract
Plasma cutting emerged as a novel technology during the 1950s and has since become the state-of-the-art method for precision metal cutting in industry. However, due to the high energy and temperature associated with the process, a number of potentially toxic fumes are produced. Despite the known health risks these fumes pose to users, existing studies have not comprehensively classified air plasma fume components. Hypertherm, a leading global plasma cutter manufacturer, partnered with our group to develop a scientific report that classifies these fumes. The report outlines the chemical identities and emission rates of fume components based on cut parameters, such that the information can be distributed to Hypertherm’s customers.
Two critical design parameters were identified in order to gather fume emission data: (1) create a fume capture system that collects both particulate and gaseous components and (2) develop analytical techniques to determine the identity and concentration of components. To develop design solutions for both goals, numerous trade studies and tests were conducted.
A series of trade studies resulted in an experimental setup in which metal is plasma cut in a modified sandblaster cabinet and fumes are collected as both particulates and gases. Particulates are collected by vacuuming over a series of filters and analyzed with Inductively Coupled Plasma Mass Spectrometry (ICP-MS). Gases are collected by extracting samples into inert Tedlar bags and analyzed with NO and NO2 sensors.
Results of this study indicate significant quantities of respirable Cr, Mn, Ni, Cu, Pb, and NO2 that exceed defined OSHA health standards by up to 500% after fewer than 10 minutes of mild (ATSM A36) and stainless steel (SS303) cutting in most unventilated environments. The majority of emitted particulates are also found to be in the smallest size range of 0.2-0.45µm: penetrating industry-standard respirators. Emission rate is observed to increase with the amperage cut parameter, while metal thickness shows no clear trend except when combined with certain amperages. Finally, the cutting of stainless steel is shown to emit over twice the quantity of dangerous and respirable particulates relative to mild steel emissions, while aluminum (Al 6061-T6) emissions are nearly negligible.
These results reinforce the importance of ventilation and mitigation systems in all cutting environments using steel, irrespective of personal protective equipment (PPE) respirator use. Furthermore, results suggest that plasma cutting operators should take into consideration cut parameters, especially amperage, in attempting to minimize exposure to air plasma fumes.
Additional testing is recommended to increase the statistical power of the results and to examine additional parameters such as more metal types and different plasma cutting system models. To further examine the composition of the particulates, specifically oxidation states, we recommend using electrochemical analysis. An investigation into gas storage and gas degradation would be required to better analyze gaseous emissions.
Level of Access
Restricted: Campus/Dartmouth Community Only Access
Dartmouth Digital Commons Citation
Je, Lisa, "Air Plasma Fume Classification" (2019). ENGS 89/90 Reports. 16.
https://digitalcommons.dartmouth.edu/engs89_90/16
Restricted
Available to Dartmouth community via local IP address.