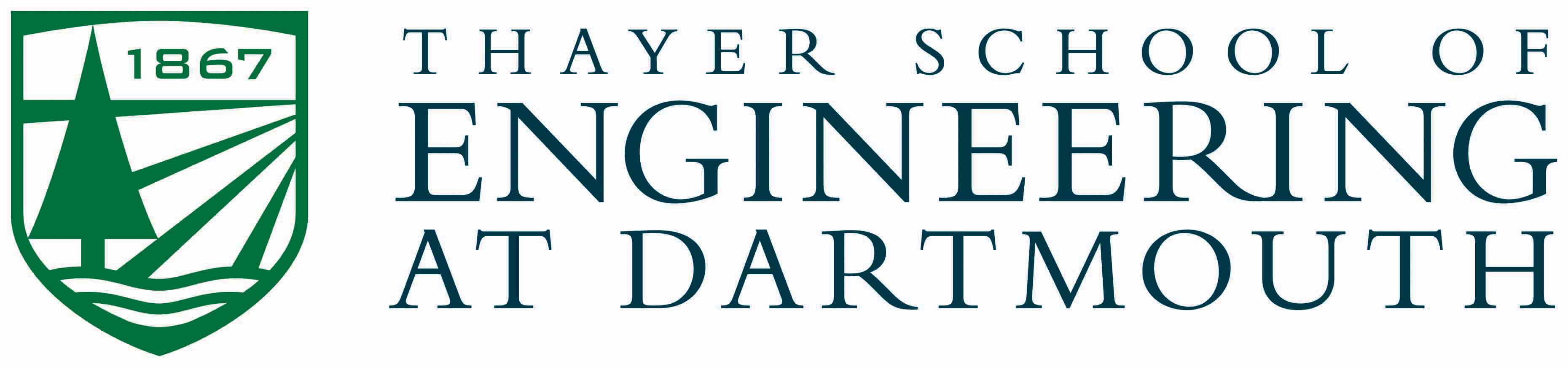
ENGS 89/90 Reports
Year of Graduation
2021
Sponsor
Mikros Technologies Claremont NH
Project Advisor
John Collier
Instructor
Solomon Diamond and Rafe Steinhauer
Document Type
Report
Publication Date
2021
Abstract
Significance: Brazing is one of the most important methods currently used in the production of the complex electronics that drive aerospace, medical, and many other industries. This process of brazing involves joining components together by melting thin metal foils between them. To ensure strong bonds between small components, braze foils are often machined into complex shapes called preforms. Since these foils are so thin (0.0005” - 0.002”) and have relatively low melting points compared to other metals, they are often difficult to cut accurately without either damaging them by clamping or causing them to warp from the heat added during machining. Other methods such as laser cutting require expensive machinery or outsourcing to larger companies, so it is more practical to search for a solution that allows smaller companies to machine in-house with a standard CNC Mill.
Problem Definition: Before we started our project, Mikros had already been developing the Ice Chuck, which keeps braze foils cold and secured during CNC milling by freezing them in a flat sheet of ice lying on a thin copper plate. After machining, the ice is melted and the machined foils are easily removed. The freezing and thawing of the ice was driven by a thermal system consisting of a series of thermoelectric coolers (TECs) and a pattern of shallow grooves cut into the top of the baseplate, where water flowing from the chiller acted as a heatsink to dissipate the heat from the TECs. The water reservoir was sealed off from the electronics by epoxy. This system had some major issues: (1) The Ice Chuck took over 6 minutes to freeze the ice before each use. (2) The TECs were cheap and prone to breaking due to thermal cycling. (3) The epoxy seal made the Ice Chuck difficult to service and would often crack, causing water to leak. The previous iteration of the Ice Chuck was not a reliable solution for Mikros to machine braze foil preforms because of its long freezing time due to an inefficient heat sink, low durability due to both water leakage from the chiller and overexertion of the TECs from thermal cycling, and lack of serviceability due to the epoxy seal.
Technical Solution: Our solution strategy was influenced both by the problems stated above and by the following specifications given to us by our sponsor: (1) The freezing time should be less than 2 minutes so the Ice Chuck can be used efficiently. (2) The TECs must last for more than 1000 cooling/heating cycles and the O-ring seal must be leak-proof to ensure durability. (3) The TECs must be easily replaceable and the Ice Chuck should be easily serviceable overall. In order to meet these specifications, we made five major changes: (A) We upgraded from the TECs in the previous iteration to models designed specifically to endure thermal cycling in order to improve durability. (B) We replaced the epoxy seal with an o-ring seal to prevent water leakage and improve serviceability. (C) We replaced the plastic 2D channel heat sink with a metal 3D pin-fin heat sink to reduce the freezing time by improving heat transfer capabilities. (D) We employed connectors in our electrical setup to improve serviceability by making TEC replacement much easier. (E) We decreased the Ice Chuck length by 5 inches (decreased working area by 20 in2) in order to lighten the thermal load on the TECs and heat sink to decrease the overall freezing time. These changes enabled us to achieve all three of the primary specifications and to deliver an updated Ice Chuck prototype that is functional, durable, and serviceable enough to be a long-term solution allowing Mikros to effectively machine braze foils in their own facilities.
Societal Context: The Ice Chuck alleviates the cost of a traditionally expensive and demanding manufacturing technique for small businesses such as Mikros. Rather than outsource a crucial component that can determine whether a part succeeds or fails, Mikros can design and produce braze foil preforms in-house. Without external order constraints, such as bulk-order requirements, engineers have greater design freedom. Our solution will also reduce the time delay between part design and fabrication by bringing another element of part production in-house, bypassing limitations due to bulk ordering. The Ice Chuck challenges the status quo of CNC milling by pushing the presumed boundaries of conventional milling dimensions. By reducing operations costs, promoting greater design freedom, and helping expedite production, the Ice Chuck opens the door to new possibilities in all the exciting, rapidly growing industries that rely on brazing.
Level of Access
Restricted: Campus/Dartmouth Community Only Access
Dartmouth Digital Commons Citation
Chavez, Joseph; Putter, Joshua; Ram, Ledane; and Washington, Nicholas, "The Ice Chuck" (2021). ENGS 89/90 Reports. 32.
https://digitalcommons.dartmouth.edu/engs89_90/32